Analyzing Asphalt Cost-effectiveness in Commercial Settings
Published on: April 8, 2025 | Last Updated: April 14, 2025
Written By: George Voss
Asphalt’s cost-effectiveness in commercial settings comes from low installation costs ($2-$5 per square foot), 15-20 year lifespan, and simple maintenance. Unlike concrete ($4-$10 per square foot), asphalt requires fewer repairs and allows faster installation—critical for minimizing business disruptions. Budget planning benefits from predictable upkeep: sealcoating every 3-5 years costs $0.15-$0.25 per square foot, preventing costly structural damage.
This article breaks down asphalt’s financial advantages for commercial projects. Compare material costs against concrete and alternatives. Explore how project size, regional pricing, and design choices impact budgets. Learn maintenance strategies to extend pavement life. Review real-world case studies from retail parking lots to industrial driveways. Get answers to common cost questions and pricing data for 2024 projects.
Comparing Asphalt to Other Commercial Paving Materials
Business owners weigh cost, use, and lifespan when picking paving. Asphalt and concrete lead the race. Each brings pros and cons for cash spent now versus later.
Cost Of Asphalt Vs. Concrete in Commercial Applications
Two costs matter: first install and long-term fixes. Asphalt often costs less up front. But concrete may need less care over time. For busy sites like lots or roads, speed and ease of fixes tilt the scale.
Initial Install Costs
Asphalt runs $2.50-$4.00 per sq ft. Concrete hits $4.00-$6.00. Why? Asphalt needs less prep, sets in 1-2 days. Concrete takes 7 days to cure. Crews work faster with asphalt, slashing labor fees. Hot mix asphalt (HMA) with PG 64-22 binder is common for its balance of flow and strength.
Long-Term Care Costs
Asphalt needs seal coats every 3-5 years ($0.15-$0.25 per sq ft). Small cracks get filled fast. Concrete may go 10+ years without care. But fixing cracks or slabs costs $2-$5 per sq ft. Over 20 years, asphalt costs 20-30% less. This makes it fit for sites that can’t shut down for weeks.
Next, we break down what shapes asphalt costs—from local price swings to job size.
Key Factors Influencing Commercial Asphalt Costs
Pricing for asphalt projects in business zones shifts with material quality, labor availability, and local market conditions. PG (Performance Graded) binders and aggregate mixes directly impact upfront costs and long-term functionality.
Material and Labor Costs
Asphalt mixtures containing polymer-modified binders typically add $1.50-$3.00 per square foot but boost crack resistance. Labor accounts for 35-45% of total project budgets, with crew rates varying from $45-$75 hourly based on location.
Regional Variations in Asphalt Pricing
- Southwest: $2.80-$4.20/sq ft
- Northeast: $3.60-$5.50/sq ft
- Midwest: $3.10-$4.80/sq ft
Impact of Project Scale on Asphalt Price per Square Foot
Projects spanning 10,000+ sq ft often cut costs by 12-18% through bulk material discounts. Hot-mix asphalt (HMA) production costs drop $8-$12 per ton for orders exceeding 500 tons.
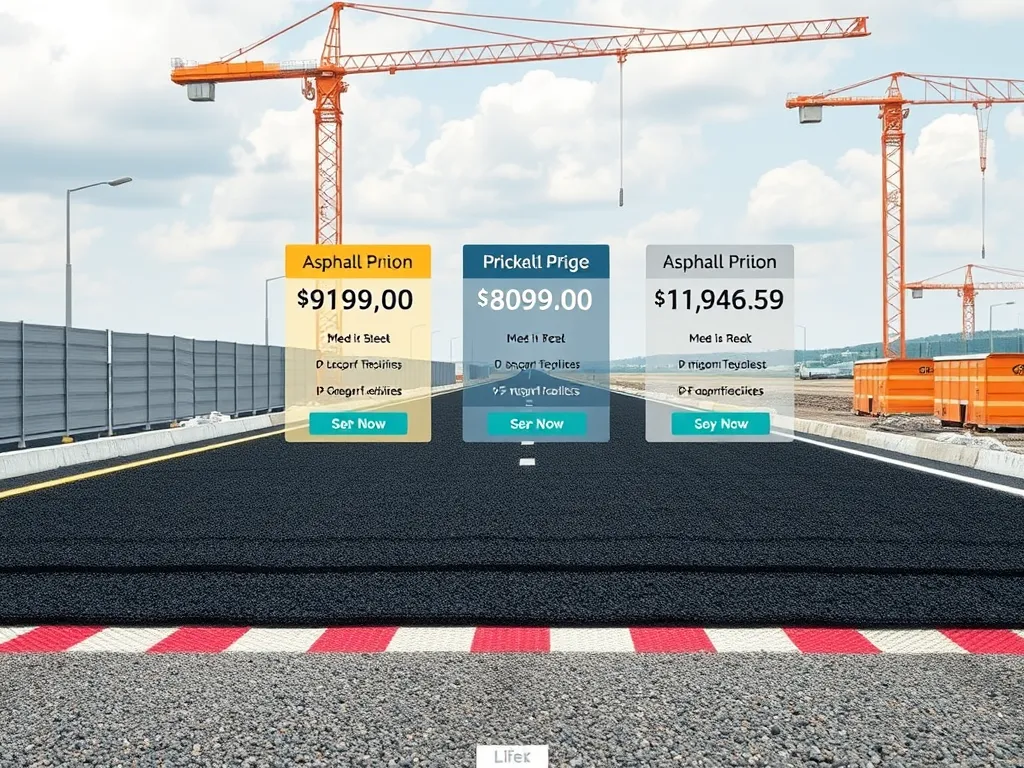
Commercial Asphalt Cost Analysis by Project Type
Parking lots and driveways dominate business paving budgets, with design choices causing significant cost fluctuations.
Cost to Pave a Commercial Parking Lot
A 50,000 sq ft lot with 3″ base and 2″ surface layer runs $145,000-$240,000. Drainage systems add $0.80-$1.20/sq ft but prevent $15,000+ in water damage repairs over 10 years.
Average Asphalt Parking Lot Cost per Square Foot
Standard installations range $2.90-$4.80/sq ft. High-traffic zones using SMA (Stone Mastic Asphalt) mixes reach $5.20/sq ft but last 22-28 years with proper care.
Commercial Driveway Installation Costs
Industrial driveways require 6-8″ compacted bases to handle truck traffic, increasing material needs by 40% vs residential builds.
20×20 Driveway Cost in Commercial Settings
400 sq ft driveways average $1,600-$2,800. Using RAP (Recycled Asphalt Pavement) cuts costs 15-22% while maintaining 8,000-10,000 PSI strength ratings.
1/4 Mile Driveway Paving Cost Considerations
1,320-foot driveways (24′ width) require 950-1,100 tons of HMA. At $85-$120/ton installed, budgets typically hit $80,750-$132,000. Geotextile fabric underlayments add $0.35/sq ft but boost longevity.
Also See: Best Practices for Asphalt Driveway Maintenance
Lifespan and Maintenance Impact on Cost-effectiveness
Properly maintained asphalt lasts 20-25 years in business zones – 3-5x longer than neglected surfaces. Annual upkeep averages $0.15-$0.30/sq ft vs $2.50-$4.00/sq ft for full replacements.
Typical Lifespan Of Commercial Asphalt Surfaces
High-traffic lots: 12-18 years Warehouse driveways: 15-22 years Service stations: 8-12 years
Preventative Maintenance Strategies to Reduce Costs
- Crack sealing ($0.10-$0.25/linear foot)
- Slurry sealing ($0.75-$1.40/sq ft)
- Infrared patching ($45-$65 per repair)
Overlay Vs. Full Replacement Cost Comparison
2″ overlays cost $1.80-$3.20/sq ft vs $3.50-$6.00/sq ft for full-depth reconstruction. Structural assessments using FWD (Falling Weight Deflectometer) testing ($1,200-$2,500) determine viable options.
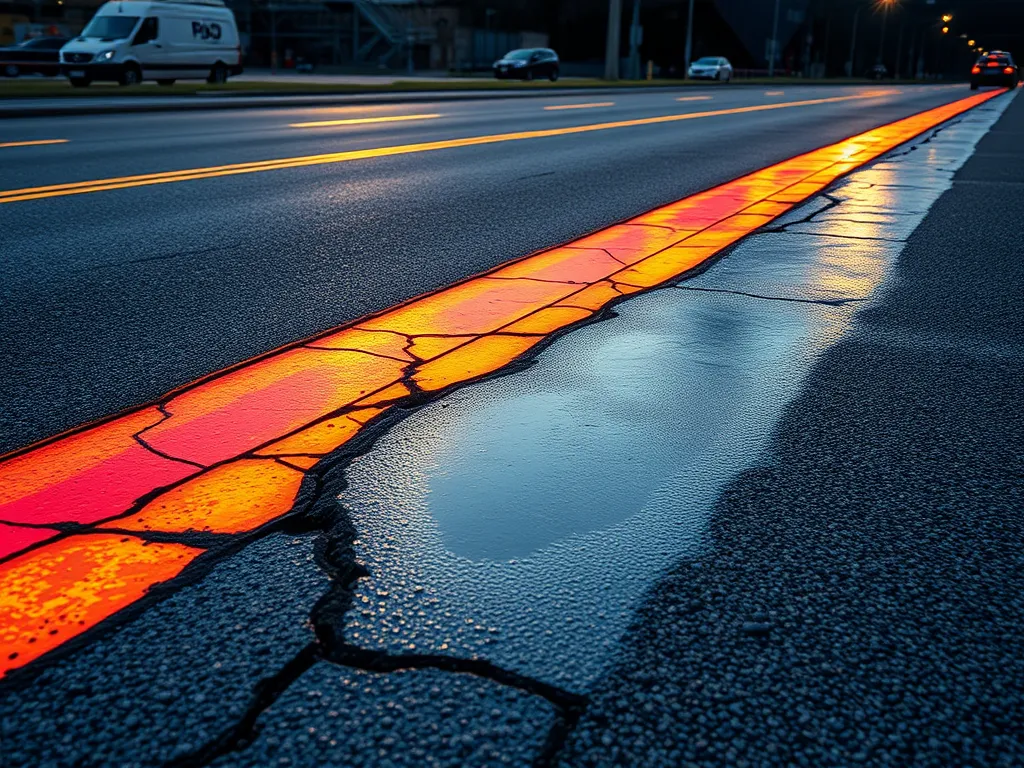
Real-world Applications Of Cost-effective Asphalt
Actual project data shows how strategic asphalt use cuts business costs while maintaining functionality.
Case Study: High-traffic Retail Parking Lot Installation
A Midwest shopping center saved 18% ($48,000) using a PG 76-22 binder mix on its 32,000 sq ft lot. The design handles 2,400 daily vehicles with 7-year warranty protection.
Case Study: Warehouse Facility Driveway Optimization
A Pennsylvania logistics hub reduced paving costs 27% by combining 30% RAP materials with 8″ crushed stone base. The $187,000 project withstands 80,000-pound trucks daily since 2018.
Addressing Common Commercial Asphalt Cost Concerns
Market shifts and project specs significantly affect budgeting accuracy for business paving jobs.
Current Asphalt Binder and Material Pricing
July 2024 spot prices: • PG 64-22: $585-$620/ton • #57 Stone: $18-$24/ton • Liquid Asphalt Cement: $680-$715/ton
Residential Vs. Commercial Asphalt Cost Differences
Business projects run 35-60% higher due to: • Thicker structural designs (6″ vs 3″ bases) • ADA-compliant features • Heavy-duty compaction requirements
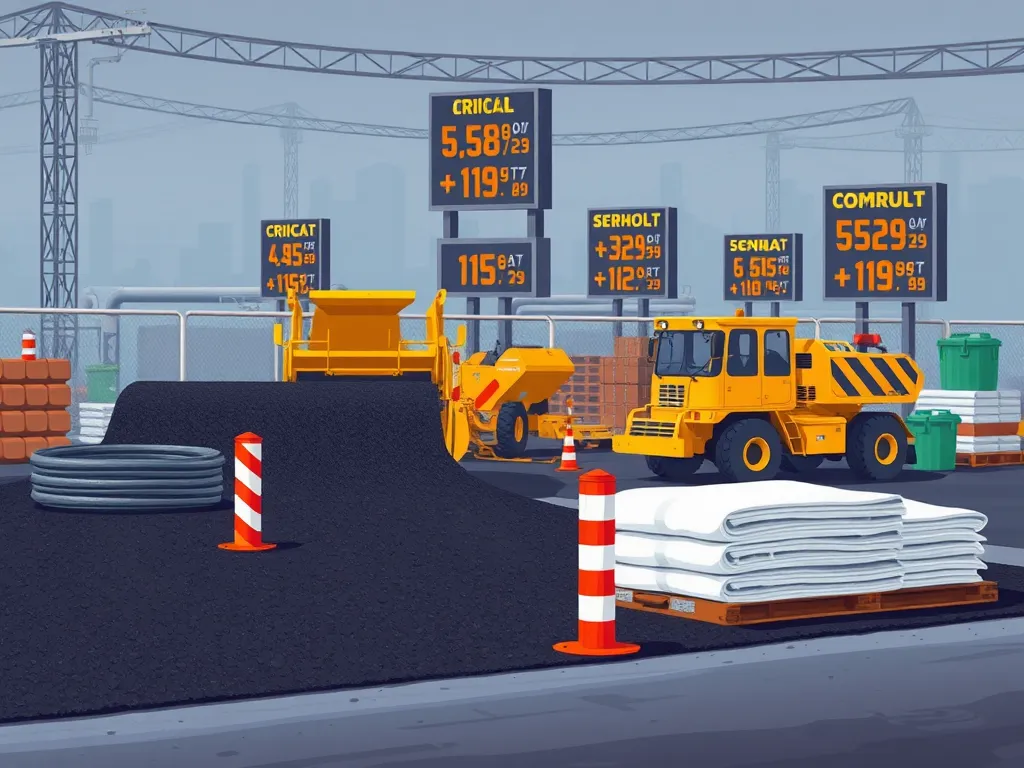
FAQs: Asphalt Cost-effectiveness in Commercial Environments
Is Asphalt Cost-effective for Commercial Applications?
Asphalt provides 40-50% lower initial costs vs concrete, with faster installation (2-4 days vs 7-10 days) reducing business downtime.
How Much Does Commercial Asphalt Cost Per Square Foot?
Current national averages: $3.20-$5.50/sq ft installed. Pricing includes 2″ surface, 4″ base, and compaction.
What is the Cost Difference Between Overlay and Replacement?
Overlays save 55-70% upfront but last 8-12 years vs 20+ years for full-depth builds. Life-cycle costing often favors full replacements for heavy-use zones.
How Does Asphalt Cost Compare to Concrete for Driveways?
Asphalt runs $3.50-$6.00/sq ft vs $8-$15 for concrete. Annual sealing adds $0.15/sq ft but prevents $2.80/sq ft in tripping hazard repairs.
What Factors Affect Commercial Asphalt Project Pricing?
- Local aggregate availability
- Fuel surcharges ($0.12-$0.18/ton/mile)
- Traffic control needs
- Drainage infrastructure
Upcoming analysis explores tax incentives and warranty options that further boost asphalt’s fiscal viability for business properties.
Commercial Asphalt Cost Analysis by Project Type
Project size and use shape asphalt costs in commercial work. We break down key pricing factors for common builds.
Cost to Pave a Commercial Parking Lot
Parking lots need thick asphalt layers (3-4″) for truck traffic. Base prep adds $1.50-$3 per sq ft to total costs.
Average Asphalt Parking Lot Cost per Square Foot
Expect $2.50-$4.50 per sq ft installed. Hot mix asphalt (HMA) with PG 64-22 binder works best. Costs vary by:
- Regional material prices ($90-$150/ton)
- Drainage needs (curbs, catch basins)
- Striping and safety markings
Commercial Driveway Installation Costs
Heavy truck traffic needs 6-8 inch bases. Stone subgrades prevent cracks in high-load areas.
20×20 Driveway Cost in Commercial Settings
A 400 sq ft drive runs $1,200-$2,000. Use polymer-modified asphalt for delivery docks. Add $500-$800 for slope grading.
1/4 Mile Driveway Paving Cost Considerations
Long drives (1,320 ft) need crew rotations. Budget $35,000-$75,000. Save 12% with recycled asphalt (RAP) mixes. Add 8-10% for cold weather paving.
Smart project planning cuts asphalt costs while meeting load needs. Next, we explore how maintenance extends pavement value.
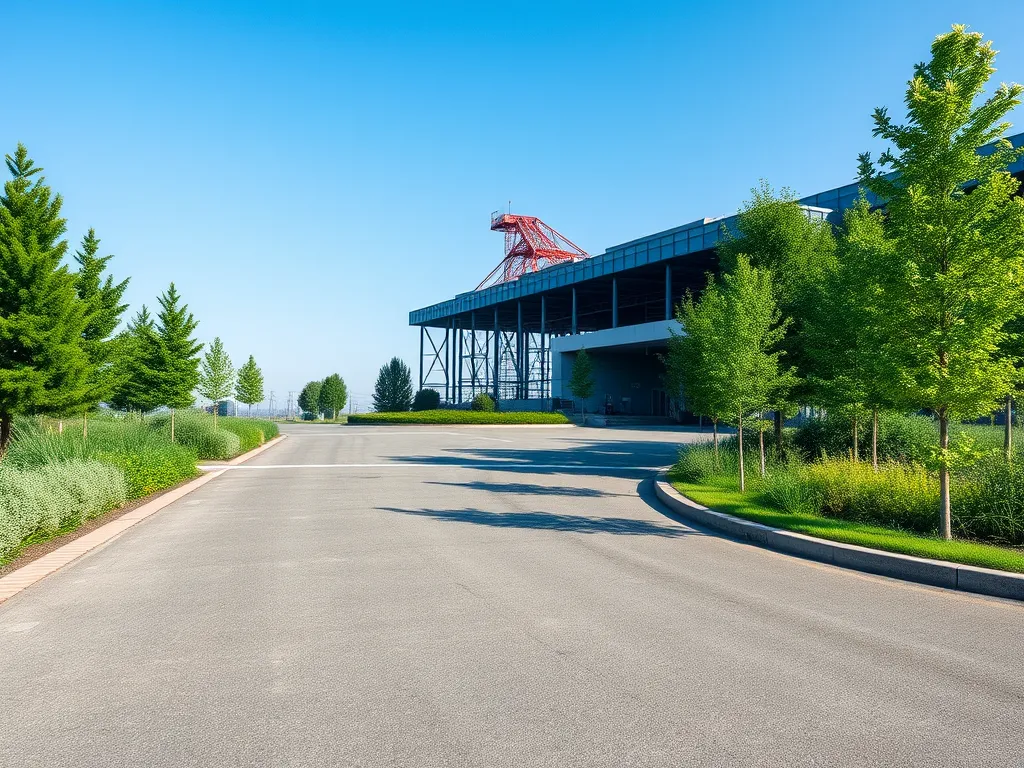
Lifespan and Maintenance Impact on Cost-effectiveness
Commercial asphalt surfaces built to last typically function 15-25 years with proper care. Climate, traffic loads, and base preparation directly impact longevity. High-grade PG 64-22 binders boost rut resistance in warm zones, while polymer-modified mixes handle heavy truck traffic. Using 30-40% recycled asphalt pavement (RAP) cuts material costs without sacrificing structural capacity.
Typical Lifespan Of Commercial Asphalt Surfaces
Parking lots in mild climates average 20 years with annual traffic under 500 cars daily. Distribution centers with constant semi-truck traffic might require resurfacing every 12 years. A 2023 National Asphalt Pavement Association study found commercial lots with routine maintenance last 53% longer than neglected ones. Lifecycle cost analysis shows annualized spending drops from $0.85/sf to $0.38/sf when planning for 25-year use.
Preventative Maintenance Strategies to Reduce Costs
- Crack sealing ($0.15-$0.35/sf) applied within 6 months of formation stops water intrusion
- Sealcoating every 2-4 years ($0.18-$0.30/sf) blocks UV oxidation
- Infrared patching fixes localized damage at 40% less cost than traditional methods
Proactive care can delay full replacements by 7-10 years. A 20,000 sf lot spending $4,500 on sealcoating avoids $45,000 in reconstruction costs over 15 years.
Overlay Vs. Full Replacement Cost Comparison
Asphalt overlay costs $2.50-$4.00/sf versus $4.50-$7.00/sf for full-depth replacement. Overlays work when existing pavement has:
- Base layer integrity intact
- Surface cracks under 1/4″ width
- No drainage issues
Structural failures demand full removal. A 50,000 sf lot overlay saves $75,000-$125,000 compared to full rebuild. Hybrid solutions combining 2″ overlay with targeted base repairs offer mid-range pricing at $3.80-$5.20/sf.
Upcoming analysis of actual projects demonstrates how strategic planning maximizes paving budgets.
Real-world Applications Of Cost-effective Asphalt
Practical asphalt installations show how its financial and functional benefits work in action. Two commercial projects highlight distinct approaches to maximizing savings without cutting quality.
Case Study: High-traffic Retail Parking Lot Installation
A 75,000 sq ft big-box store parking lot in Texas used PG 64-22 binder asphalt with a 4″ base and 2″ surface layer. Initial costs hit $2.85/sq ft – 32% lower than concrete bids. Annual crack sealing and sealcoating at $0.18/sq ft added up to $13,500 yearly. Over 12 years, total costs stayed below $4.10/sq ft, while a comparable concrete lot would’ve required $6.20/sq ft for full-depth repairs by year 10.
Cost Factor | Asphalt | Concrete |
---|---|---|
Installation (2023) | $213,750 | $315,000 |
10-Year Maintenance | $135,000 | $247,500 |
Total (12 Years) | $348,750 | $562,500 |
Case Study: Warehouse Facility Driveway Optimization
A Midwest logistics hub saved 19% on a 1/4-mile truck route by choosing 6″ full-depth asphalt over 8″ composite pavement. Using 30% RAP (Recycled Asphalt Pavement) brought material costs down to $82/ton. Cross-drainage slopes and open-graded shoulders minimized water damage, cutting repair needs by 40% compared to prior designs. Lifecycle tracking shows $15.70/ft annual costs vs $23.40/ft for concrete alternatives.
These installations prove asphalt’s financial flexibility across commercial uses. Up next: common budget questions from property managers planning paving projects.
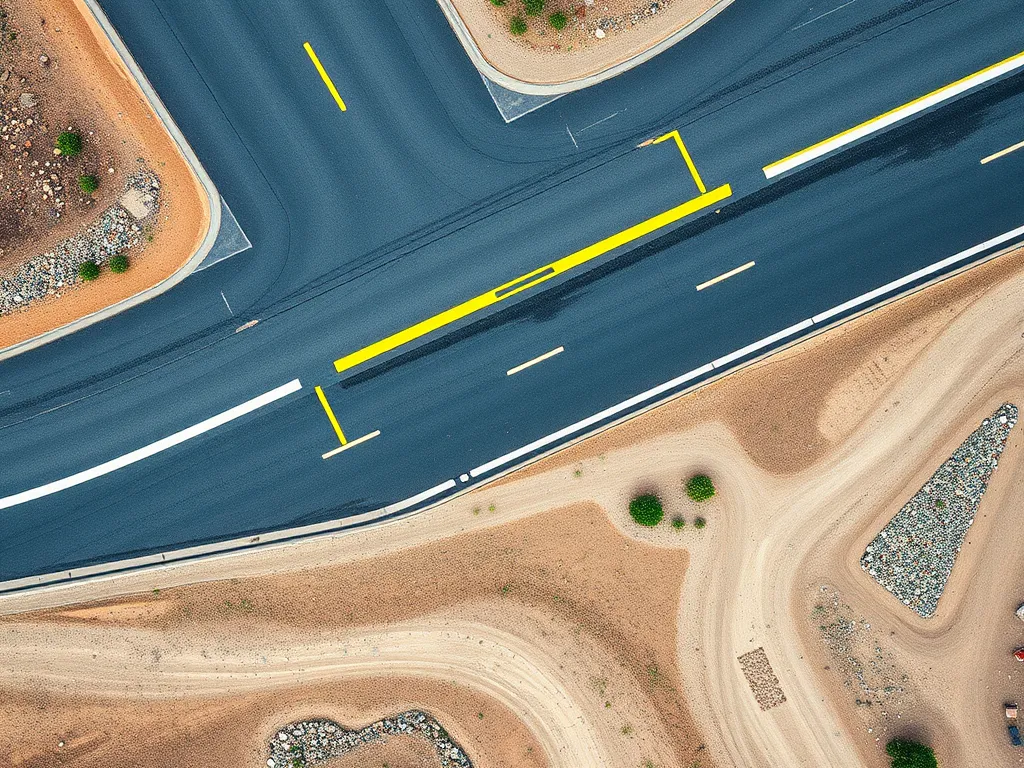
Addressing Common Commercial Asphalt Cost Concerns
Business owners evaluating pavement options need clear data on material economics and project variables. Let’s break down two critical pricing factors impacting asphalt cost effectiveness in commercial environments.
Current Asphalt Binder and Material Pricing
Asphalt binder costs (the glue holding aggregates together) directly drive project budgets. As of 2023, PG 64-22 binder – the most common type for commercial projects – ranges $85-$125/ton. Polymer-modified binders like PG 76-22 used for heavy truck traffic cost $135-$185/ton.
- Crude oil prices influence 65% of asphalt pavement costs
- Regional transportation adds $8-$15/ton within 100-mile radius
- Recycled asphalt pavement (RAP) reduces material costs by 20-35%
Commercial mix designs typically use 5% binder content – meaning a 10,000 sq ft parking lot requires 18-22 tons of binder at current asphalt prices.
Residential Vs. Commercial Asphalt Cost Differences
Commercial asphalt costs average $2.50-$4.50/sq ft versus residential’s $3.50-$6.00/sq ft. Three factors create this asphalt cost effectiveness gap:
- Scale discounts: Paving 50+ spaces cuts per-unit costs by 15-30%
- Base construction: Commercial sites use 8-12” aggregate base vs residential 4-6”
- Pavement structure: 3” minimum thickness for parking vs 2” for driveways
Load-rated designs for delivery trucks require stiffer PG binders – adding $0.40-$0.75/sq ft versus residential mixes. However, commercial projects spread these costs over larger areas.
These pricing factors set the stage for evaluating specific project types – from compact retail lots to industrial complexes requiring specialized asphalt economics.
FAQs: Asphalt Cost-effectiveness in Commercial Environments
Is Asphalt Cost-effective for Commercial Applications?
Asphalt is often considered cost-effective in commercial settings due to its lower initial costs compared to alternatives like concrete, alongside its quick installation that reduces downtime for businesses.
How Much Does Commercial Asphalt Cost Per Square Foot?
The average cost for commercial asphalt installation typically ranges from $3.20 to $5.50 per square foot, including both surface and base layers.
What is the Cost Difference Between Overlay and Replacement?
Asphalt overlays generally cost between 55-70% less upfront compared to full replacements, but they may have a shorter lifespan than complete rebuilds, making lifecycle costing an important consideration.
What Factors Affect Commercial Asphalt Project Pricing?
- Local aggregate availability and pricing variations.
- Impact of fuel surcharges for transportation.
- Any special traffic control measures necessary during construction.
- Specific drainage infrastructure requirements for the site.
How Does Asphalt Longevity Impact Overall Cost-effectiveness?
Asphalt surfaces can last 15-25 years with proper maintenance, which significantly reduces the total cost of ownership over time, making it a financially sound option for commercial projects.
Are There Maintenance Recommendations to Enhance Asphalt’s Cost-effectiveness?
Regular maintenance activities such as crack sealing, sealcoating, and timely repairs can extend the lifespan of asphalt, reducing the need for costly full replacements.
What Role Does the Choice Of Asphalt Mix Play in Cost-effectiveness?
Choosing the right mix can greatly influence performance and longevity, with options like polymer-modified asphalt providing better resistance against wear and tear, thus potentially lowering future maintenance costs.
How Can Project Size Influence Asphalt Costs?
Projects that are larger in scale typically benefit from bulk material discounts and reduced labor costs per square foot, which can make asphalt paving more economical overall.
Closing Thoughts
Asphalt stands out as a cost-effective choice in commercial paving. Its initial installation costs are often lower than alternatives like concrete, and its maintenance is more manageable. Over time, asphalt delivers durability, making it an appealing option for businesses looking to optimize their investments.
Factors such as regional pricing variations and project scales play significant roles in determining overall costs. Understanding these elements helps businesses make informed decisions, ensuring they get the most value from their pavement projects.
From commercial parking lots to driveways, asphalt’s versatility shines through in real-world applications. With appropriate maintenance strategies, the lifespan of asphalt surfaces can be extended, further enhancing their cost-effectiveness.
For more insights and tools to help you with your asphalt projects, check out Asphalt Calculator USA. Make informed choices that benefit your budget and business in the long run.
Additional Resources for You:
- Huang, Y. H. (2004). Pavement Analysis and Design (2nd ed.). Upper Saddle River, NJ: Pearson/Prentice Hall.
- How to Calculate the Price of Asphalt
- Asphalt Pricing Factors: How Much Does Asphalt Cost?
- Current Asphalt Driveway Cost: A Comprehensive Pricing Guide for 2024 – Asphalt Industrial
- Commercial Asphalt Paving Cost: Expert Insights Compiled » All Star Contracting Services
Also See: Advantages Of Recycling Asphalt: Save Money & Resources