Advanced Pouring Techniques for Professionals
Published on: May 17, 2025 | Last Updated: April 14, 2025
Written By: George Voss
Advanced pouring techniques for professionals involve precise material control and specialized methods that elevate both functional beverage service and artistic creations beyond basic applications. Unlike simple pours, these methods require analyzing material behavior, environmental factors, and chemical interactions to achieve consistent results. Baristas master multi-layer latte art through milk texture control, while acrylic artists create fractal patterns by manipulating paint density and tilt angles. Key skills include viscosity adjustment, spill-free transfers, and intentional air bubble management.
This article details advanced pouring strategies across industries. Explore core methods like dirty pours combining multiple colors in one vessel and dynamic multi-pour sequences for geometric designs. Learn cell formation mechanics using Floetrol additives at 30-40% mix ratios and alcohol-based flow disruptors. Compare cup types from standard tumblers to angled pitchers for specific pattern outcomes. Get temperature guidelines for optimal material flow (65-75°F ideal) and tilt board setups for directional control. Includes safety protocols for solvent disposal and ventilation requirements.
Introduction to Professional-grade Pouring Methods
Professional-grade pouring bridges technical precision with creative execution across industries. From mixology to acrylic art, advanced pouring techniques separate amateurs from pour masters through controlled material flow and pattern mastery.
Defining Advanced Beverage and Artistic Pouring
Advanced beverage pouring combines spill-free mechanics with showmanship – think layered cocktails with clean density separation or 2-ounce free pours within 5% variance. Artistic pouring focuses on manipulating acrylics/resins using gravity, additives like Floetrol (a pouring medium), and tilt techniques to create organic cells and lacing effects. Both demand millimeter-level control over stream angles, pour heights (6-10″ optimal for paint), and material temperatures (60-75°F ideal for viscosity).
Why Expert Pouring Skills Matter for Professionals
In bartending, precise pours directly impact drink consistency and profitability – a 0.25oz overpour across 100 cocktails wastes $15-$30 in premium liquor. For artists, uneven paint distribution or failed cell formation can ruin $50-$200 worth of materials per canvas. Mastery reduces material waste by 18-22% while enabling complex designs like Dutch pours or swipe technique marbling. Speed matters: Top mixologists achieve 2.5-second measured pours without spilling, while acrylic pros complete large-scale pours before paint skins form (7-12 minutes working time).
Ready to explore the core techniques driving these results? Let’s break down the methods transforming basic pours into gallery-worthy finishes and bar-ready precision.
Core Advanced Pouring Techniques
Mastering advanced pouring requires precision, timing, and adaptability. These methods transform basic pours into controlled artistry across industries.
The Dirty Pour Technique Explained
The dirty pour stacks layered materials in one vessel before release. Used in acrylic art and multi-layered beverages, this method creates organic patterns through strategic material layering. Bartenders apply it for gradient cocktails, while artists achieve marble-like swirls with 3-5 paint layers. Success depends on viscosity control – acrylics need 30-40% Floetrol, while liquor pours demand exact 1.5oz jigger measurements.
Step-by-Step Dirty Pour Execution
Step | Art Application | Beverage Application |
---|---|---|
1. Prep | Mix paints with 2:1 medium ratio | Chill glassware to -2°C |
2. Layer | Alternate colors in cup | Float liquors by density (0.9-1.2 g/cm³) |
3. Release | 45° tilt, continuous flow | Double-strain through Hawthorne |
Dynamic Multi-pour Strategies
Simultaneous pours from multiple vessels create intricate interactions. Artists use 3-7 cups for cells and lacing; bartenders pour twin streams for split-base cocktails. Key tools include angled goblets for paint and weighted 750ml decanters for liquor. Maintain 10-12″ pour height for optimal aeration without splatter.
Hand-pouring Mastery for Precision
Freehand pouring requires calibrated grip strength and wrist rotation. Professionals pour 1oz/sec with ±0.1oz variance. Train with 500ml graduated cylinders: 80% accuracy in 3 weeks. For acrylics, master the “feather stop” – halting flow without drips using thumbnail pressure on cup rims.
These foundational skills set the stage for specialized methods like cell creation and alcohol-based flow control – critical for gallery-ready pours or craft cocktail consistency.
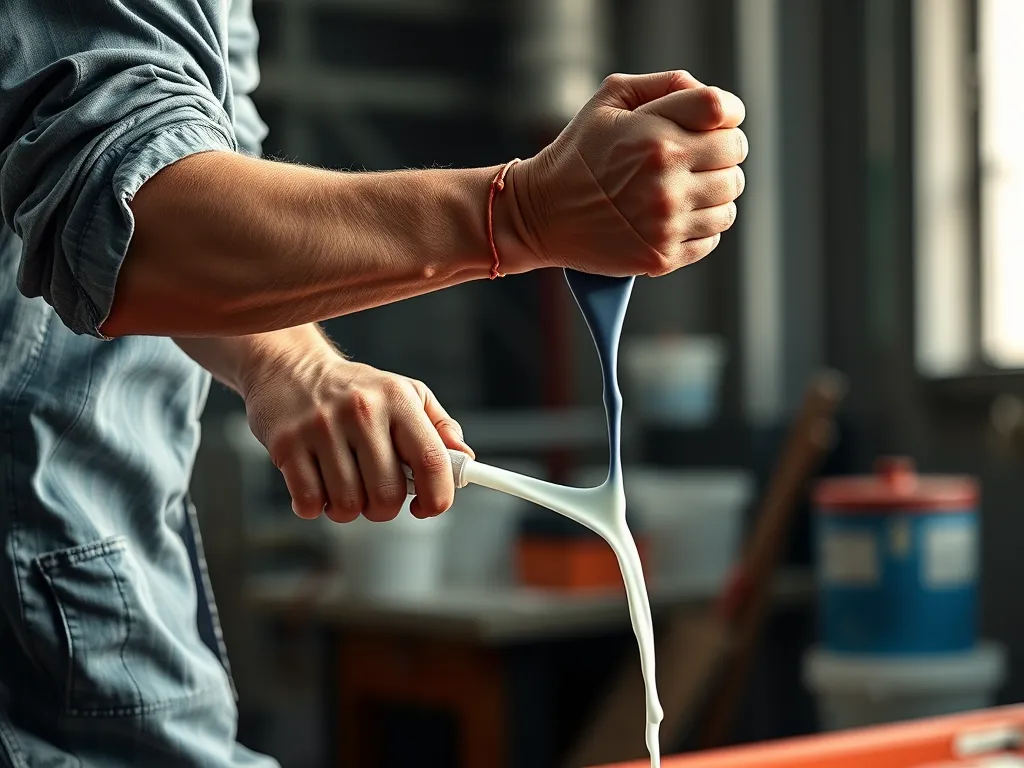
Specialized Methods for Optimal Results
Professionals elevate their work through precise material science paired with innovative application methods. Three core strategies dominate modern cell formation: chemical additives, flow modifiers, and silicone-free approaches.
Creating Cells in Acrylic Pouring
Cells form when varying paint densities interact, producing distinct circular patterns. While novices rely on luck, pour masters control variables like medium viscosity, additive timing, and tool selection to direct outcomes.
Floetrol Ratios for Enhanced Cell Formation
This paint conditioner modifies flow without compromising pigment strength. Optimal mixtures range from 1:1 to 2:1 paint-to-Floetrol ratios. Higher concentrations (beyond 2.5:1) risk structural weakness—balance with 10-15% water for large-scale works. Tests show 1.75:1 blends yield 2-4mm cells when combined with 2% isopropyl alcohol.
Rubbing Alcohol Effects on Paint Flow
Isopropyl alcohol (91% purity) acts as a cell catalyst by breaking surface tension. Introduce 3-5 drops per ounce of mixed paint during the final stir phase. Note: exceeding 7% alcohol content causes premature evaporation, leading to fissures in dried pieces.
Silicone-free Cell Development Techniques
Many studios now eliminate silicone due to surface residue concerns. Proven alternatives include:
- GAC 800 polymer medium (mixed 1:3 with paint)
- Multiple pour layers with varied drying times
- Strategic torch passes during the 45-second curing window
Dutch pour methods generate organic shapes through forced air manipulation—ideal for mural-scale projects requiring uniform cell distribution.
With these methods mastered, focus shifts to executing them with exacting physical control. Next, we examine mechanics for maintaining precision during complex pours.
Also See: Advanced Asphalt Additives for Safety: Improving Durability
Professional Pouring Skills and Control
Sharp control sets pros apart. Master spill-free flow, layered pours, and temp shifts for next-level work.
Spill-free Pouring Mechanics
Grip matters. Hold vessels at 45° for steady flow. Bartenders use “free pour” counts (1-2-3-4 for 1.5 oz). Artists tilt cups 1″ above canvas. Both keep elbows tight – no wrist flicks. Try silicone spouts for thin streams. Track flow rates: 4 oz/sec max for drinks, 6 oz/sec for paint.
Layered Pouring for Complex Patterns
Stack colors without mix-ups. Bartenders layer liquors by weight – heavy syrups first (1.3g/cm³), then mid-proof spirits (0.95g/cm³). Paint pros use density splits: add Floetrol® (40% mix) to light hues, 90% isopropyl alcohol to dense shades. Wait 30 sec between layers. Test combos first – some pigments bleed.
Temperature and Tilt Manipulation
Heat thins, cold thickens. Chill glass rims to slow drink pours (34°F ideal). Warm acrylics to 75°F for better cell spread. Tilt surfaces 15-20° for paint flow control. Bartenders “roll” bottles to mix layers. Pros check room temp – 68-72°F stops rush pours.
Ready to gear up? The right tools make these moves click.
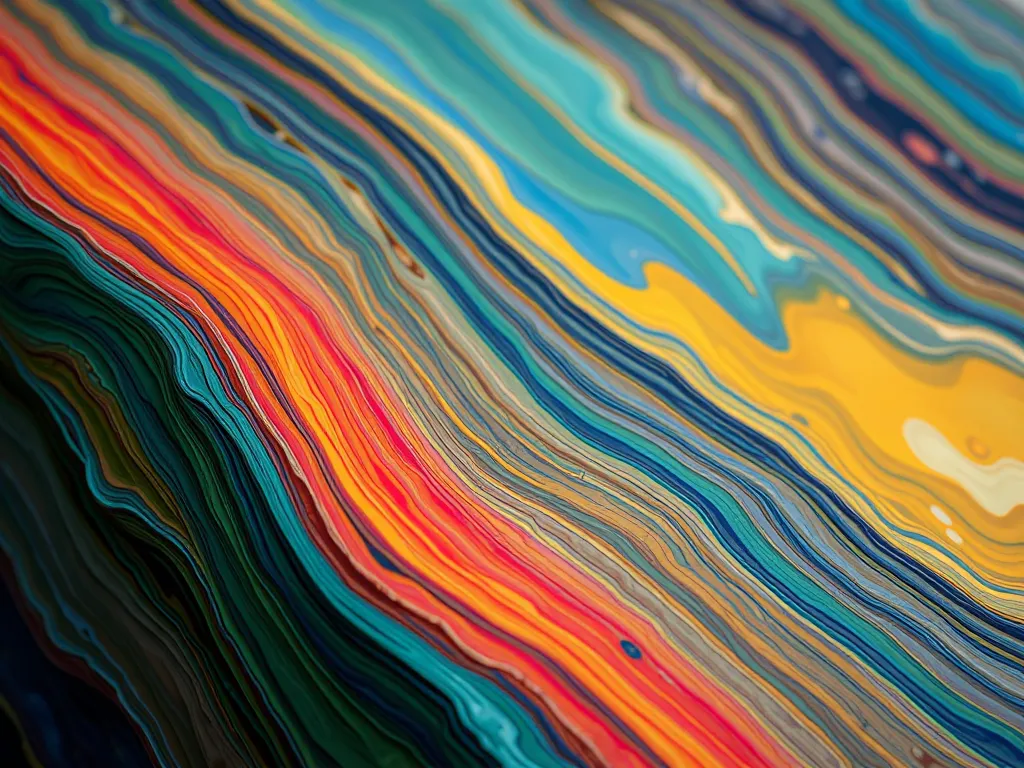
Tools and Mediums for Expert Pouring
Mastering advanced pouring techniques requires pairing skill with purpose-built materials. The right combinations unlock precise control across both artistic and beverage applications.
Selecting Pouring-friendly Paints
High-flow acrylics with 5-15 cP viscosity work best for fluid art pours. Brands like Liquitex Professional or Golden Fluid provide consistent pigmentation without clumping. Mix 2 parts paint to 1 part Floetrol—a pouring medium that improves flow while maintaining structural integrity. Add 1-2 drops of 100% silicone oil per 4 oz mixture to boost cell formation in acrylic works.
Essential Tools for Advanced Pour Craft
Artists need heat guns ($25-$80) set to 200-300°F for manipulating cells, while bartenders rely on stainless steel jiggers with engraved measurements (0.5-2 oz). Both fields use graduated pouring vessels: 32 oz plastic cups for layered paint pours, tapered glass cylinders for liquor with 1.5 oz/sec flow rates. Torch lighters ($8-$15) remove bubbles in resin art; angled pour spouts create clean streams in cocktail service.
Cup Types and Pouring Vessel Strategies
Dirty pour artists stack colors in 16 oz Solo cups before simultaneous release. Bartenders serving flights use 2 oz ceramic sake cups for controlled portions. For large-scale acrylic works, reusable silicone vessels with 45° angled lips reduce spillage. In mixology, double-walled metal tins maintain cocktail temperatures during multi-pour sequences.
Sharpening your toolkit prepares you for the next frontier: balancing creative results with responsible material handling.
Environmental and Safety Considerations
Mastering advanced pouring techniques demands equal attention to material stewardship and workspace safety. Professionals balancing artistic fluidity with operational responsibility yield both stunning results and sustainable practices.
Eco-friendly Disposal Of Pouring Materials
Seasoned pour artists recycle 60-70% of leftover acrylic paints through silicone-free reblending. Store excess mixtures in airtight containers for future projects. For resin-based pours, check local regulations – many facilities accept cured epoxy as non-hazardous waste if free from alcohol inks or metallic powders.
Solvent disposal follows strict protocols:
- Mineral spirits: Evaporate in sealed pans (never pour drains)
- Isopropyl alcohol: Let particulates settle, filter for reuse
- Flammable thinners: Use approved DOT containers for drop-off
Material | Disposal Method | Cost Impact |
---|---|---|
Wet acrylics | Solidify with kitty litter | $0.50/lb savings |
Cured resin | Landfill-approved chunks | $2-5/lb fees |
Ventilation and Workspace Best Practices
Professional studios maintain 100+ CFM airflow using explosion-proof fans when working with pouring mediums containing VOCs (volatile organic compounds). Cross-ventilation setups prevent fume buildup – position intake vents low, exhaust vents high.
Critical PPE for expert pouring techniques:
- NIOSH-approved N95 respirators ($40-$120)
- Chemical-resistant gloves (8-12 mil thickness)
- Anti-static aprons (prevents dust attraction)
Store Floetrol and pouring oils in fire-rated cabinets at 50-77°F. Monitor humidity below 60% to prevent premature curing during multi-pour projects.
These protocols let pour masters focus on technique refinement while maintaining studio integrity. Next, we’ll address frequent technical queries that arise during high-level pouring work.
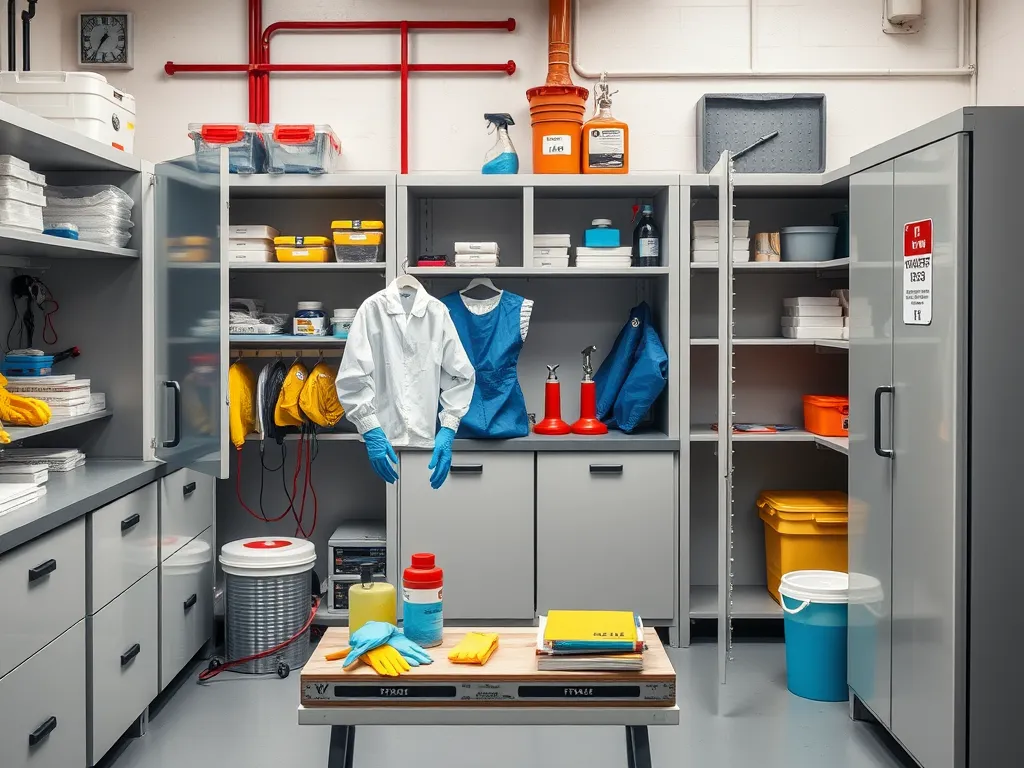
FAQs: Advanced Pouring Techniques
What Tools Are Essential for Advanced Pouring Techniques?
Essential tools include high-flow paints, graduated pouring vessels, heat guns for cell manipulation, stainless steel jiggers for precise measurements, and angled pour spouts for clean streams. Each tool is designed to enhance the precision and effectiveness of your pouring techniques.
How Do I Maintain Spill-free Pouring in My Practice?
To ensure spill-free pouring, maintain a 45° angle while pouring, and keep your elbows close to your body to stabilize your grip. Utilize a consistent pouring speed and consider using silicone spouts to control flow for both liquid and acrylic materials.
What Role Does Temperature Play in Advanced Pouring Techniques?
Temperature is crucial as it affects the viscosity of your materials. Warmer paints flow more easily, ideal for creating cells and smooth distributions, while chilled vessels can slow down pour rates, helping to achieve cleaner layers in cocktails.
Can I Use Silicone in My Acrylic Pouring, or Are There Alternatives?
While silicone is commonly used for cell creation, many artists are shifting towards silicone-free techniques. Alternatives include using GAC 800 polymer medium or employing various pour layers with different drying times, which can yield comparable results without the residue issues associated with silicone.
How Can I Ensure Even Color Distribution During Layered Pours?
To achieve even color distribution, layer colors based on their density, with heavier liquids at the bottom. Allow time between layers for pigments to stabilize and avoid mixing. Testing combinations beforehand can help prevent unwanted bleeding.
What Safety Precautions Should I Consider During Pouring?
Safety precautions include ensuring proper workspace ventilation, wearing N95 respirators when working with VOCs, using chemical-resistant gloves, and storing hazardous materials in fire-rated cabinets. Always follow local regulations for disposal of materials as well.
Closing Thoughts
Mastering advanced pouring techniques elevates any project, enhancing both aesthetic appeal and functional precision. From the dynamic dirty pour to meticulous layered approaches, these skills empower professionals to achieve stunning results. By understanding the interplay of mediums, methodical manipulation, and artistic strategies, one can truly transform ordinary surfaces into captivating masterpieces.
Investing time in refining your pouring techniques pays off significantly. Remember, the right tools, eco-friendly practices, and safety measures are paramount. Embrace continual learning and experiment with new methods to stay at the forefront of your craft.
For more tips and resources on advanced pouring techniques, check out Asphalt Calculator USA.