Advanced Asphalt Testing Techniques: Precision, Standards, and Equipment
Published on: May 15, 2025 | Last Updated: April 14, 2025
Written By: George Voss
Advanced asphalt testing techniques are high-precision methods used to evaluate pavement materials under real-world conditions. Unlike traditional approaches that rely on basic physical tests, these modern methods—like Dynamic Shear Rheometer (DSR) testing and Multiple Stress Creep Recovery (MSCR)—analyze asphalt’s elasticity, rutting resistance, and low-temperature performance. They ensure roads meet strict durability standards, improve safety, and comply with regulations like AASHTO and ASTM. Engineers now use advanced tools to predict how asphalt behaves under traffic loads, temperature swings, and moisture exposure.
This article breaks down the science behind advanced asphalt testing. You’ll learn core principles driving these methods, key equipment like infrared spectrometers and hydraulic load frames, and how standards like Superpave shape modern practices. We’ll also cover lab procedures, field testing innovations, and eco-friendly practices reducing waste in asphalt labs.
Core Principles Of Advanced Asphalt Testing
Advanced asphalt testing techniques analyze material behavior under varied conditions to predict pavement performance. These methods go beyond basic quality checks, measuring precise mechanical properties linked to real-world stress factors. The scope spans lab-based simulations, field assessments, and digital modeling across new builds, recycled mixes, and maintenance projects.
Definition and Scope
Modern testing targets three areas: thermal response, load resistance, and aging effects. Engineers use tools like dynamic shear rheometers or infrared spectrometers to assess binder elasticity, mixture density, and surface friction. Tests follow strict protocols from AASHTO, ASTM, or the Superpave system, ensuring data aligns with regional climate needs and traffic volumes.
Role in Modern Pavement Engineering
Rutting, cracking, and moisture damage cost U.S. agencies $14 billion yearly in repairs. Advanced tests slash these risks by identifying weak mixes before installation. For example, MSCR trials measure how binders recover from heavy truck loads at 140°F, while ITSM tests verify stiffness modulus to prevent cold-weather fractures. Such data lets engineers adjust aggregate gradation or PG binder grades proactively.
Key Objectives: Durability, Safety, and Compliance
- Durability: MBC asphalt tests track moisture susceptibility, while BBR analysis predicts low-temperature cracking below 14°F
- Safety: Skid resistance tests using British Pendulum Numbers (BPN) ensure surfaces meet FHWA’s 35+ BPN threshold
- Compliance: Meeting ASTM D7370 for density (92-96% compaction) or AASHTO T 283 for tensile strength ratios (≥80%)
With evolving materials like polymer-modified asphalt or recycled rubber, advanced testing bridges innovation with reliability. Next, we break down the methods turning these principles into actionable data.
Key Advanced Asphalt Testing Methods
Modern asphalt testing uses precise tools to predict how pavements will hold up under stress, weather, and traffic. These methods go beyond basic checks to spot flaws before roads fail.
Dynamic Shear Rheometer (DSR) Testing
DSR tests asphalt binders like PG 64-22 or PG 76-16. It applies shear forces at temps from 46°C to 82°C to mimic road strain.
Assessing Binder Elasticity and Viscosity
By measuring phase angles and complex shear modulus, DSR shows if binders bounce back after stress or stay deformed. AASHTO T315 sets pass/fail limits for rutting risk.
Multiple Stress Creep Recovery (MSCR)
MSCR replaces old rut tests like G/sinδ. It cycles 100 creep-and-recovery steps at 0.1 kPa and 3.2 kPa stress levels.
Evaluating Rutting Resistance
High-traffic roads need ≥ 75% recovery in MSCR tests. This method spots weak binders that sag under trucks better than basic grade checks.
Indirect Tensile Stiffness Modulus (ITSM) Test
ITSM applies vertical loads to cylindrical samples at 20°C. Sensors track horizontal deformation to calculate stiffness in MPa.
Measuring Stiffness in Asphalt Mixtures
Stiff mixes (≥ 5,000 MPa) resist cracking but stay flexible. ITSM aligns with EN 12697-26 standards for lab and field cores.
Bending Beam Rheometer (BBR) Testing
BBR checks thermal cracking risk by bending binder beams at -24°C. Loads measure creep stiffness over 240 seconds.
Low-Temperature Performance Analysis
Beams must stay below 300 MPa stiffness (S-value) and have m-values ≥ 0.30 per ASTM D6648. Failing specs mean pavements crack in deep freezes.
From binder checks to mix tests, these tools shape how engineers build roads that last. Next, we break down the gear that makes these tests work.
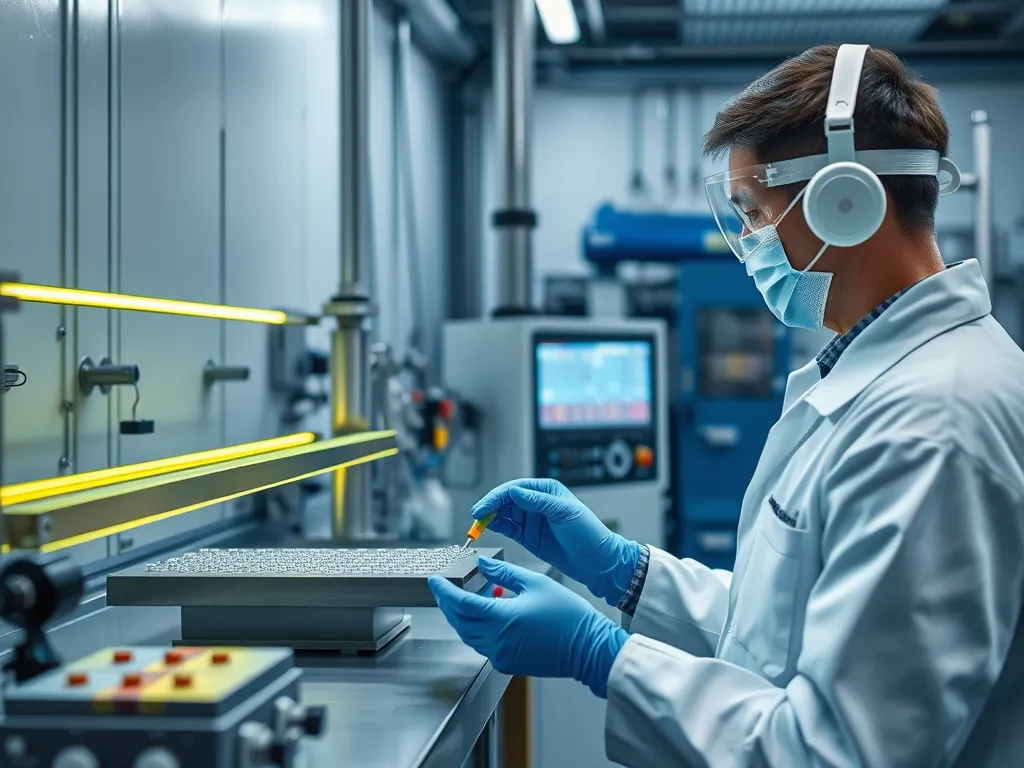
Critical Asphalt Testing Equipment
Precision tools drive accurate results in advanced asphalt pavement testing. From lab benches to job sites, specialized gear measures performance metrics critical for durable roads.
Advanced Laboratory Tools
Labs rely on cutting-edge instruments to simulate real-world stresses. These devices align with asphalt mixture testing standards like ASTM D7981 for binder grading.
Static and Dynamic Shear Rheometers
Static shear rheometers measure binder stiffness at rest, while dynamic versions test elasticity under traffic-like vibrations. Both identify PG binder grades for climate-specific mixes. Modern units achieve ±0.1% torque accuracy at temperatures from -40°F to 302°F.
Pneumatic and Hydraulic Loading Frames
These frames apply controlled forces during asphalt concrete lab tests. Pneumatic systems deliver 50 kN loads for ITSM evaluations, while hydraulic models handle 200 kN for fracture tests. Operators track strain rates down to 0.0001 mm/s via integrated LVDT sensors.
Field Testing Devices
On-site tools provide instant data during paving operations. Contractors use these to verify compliance with asphalt concrete testing standards before finalizing layers.
Portable Infrared Spectrometers
Handheld units analyze binder content in real time during asphalt tests. By scanning RAP materials, crews confirm 95-98% recycling rates within 90 seconds. Models like the ABB Titan 560 detect hydrocarbon levels at 2 cm² resolution.
Intelligent Compaction Analyzers
GPS-enabled rollers map density across pavement surfaces during asphalt engineer testing. Sensors track passes, temperature, and stiffness, creating color-coded reports showing areas below 92% density targets. Caterpillar’s CC-7 model cuts compaction time by 18% through automated pattern adjustments.
With robust equipment in play, the next layer examines how testing protocols maintain consistency across projects.
Also See: Acoustic Properties Of Porous Asphalt: Noise Reduction
Standards Governing Advanced Testing
Advanced asphalt tests rely on strict rules to ensure roads last longer and stay safe. Groups like AASHTO and ASTM set these rules. Their methods guide labs and crews in checking asphalt mix quality.
AASHTO and ASTM Protocols
AASHTO and ASTM create test steps used across the U.S. These steps check key traits like strength, bend power, and heat resistance.
AASHTO T 313: Fracture Tensile Strength
AASHTO T 313 tests how well asphalt handles cracks under stress. Labs use it to rate binders in cold zones. This method helps spot weak mixes before they fail on roads.
ASTM D7313: Elastic Recovery of Binders
ASTM D7313 checks if binders bounce back after stress. It uses a ductile test to see how much stretch the mix can take. Results predict rutting risk in high-heat areas.
Superpave Performance Grading System
The Superpave system ranks asphalt by how it acts in real heat and traffic. It ties binder grades to site temps and truck loads. This stops rutting in summer and cracks in winter.
Integration with Advanced Test Methods
Superpave now works with tools like DSR and BBR tests. For example, DSR data sets the PG grade for heat flow. BBR cold tests align with low PG ratings. This mix boosts road life by 15-20% in harsh zones.
With these standards in place, teams can shift focus to real-world use. The next step? Applying these tests in the field and lab with the right tools and steps.
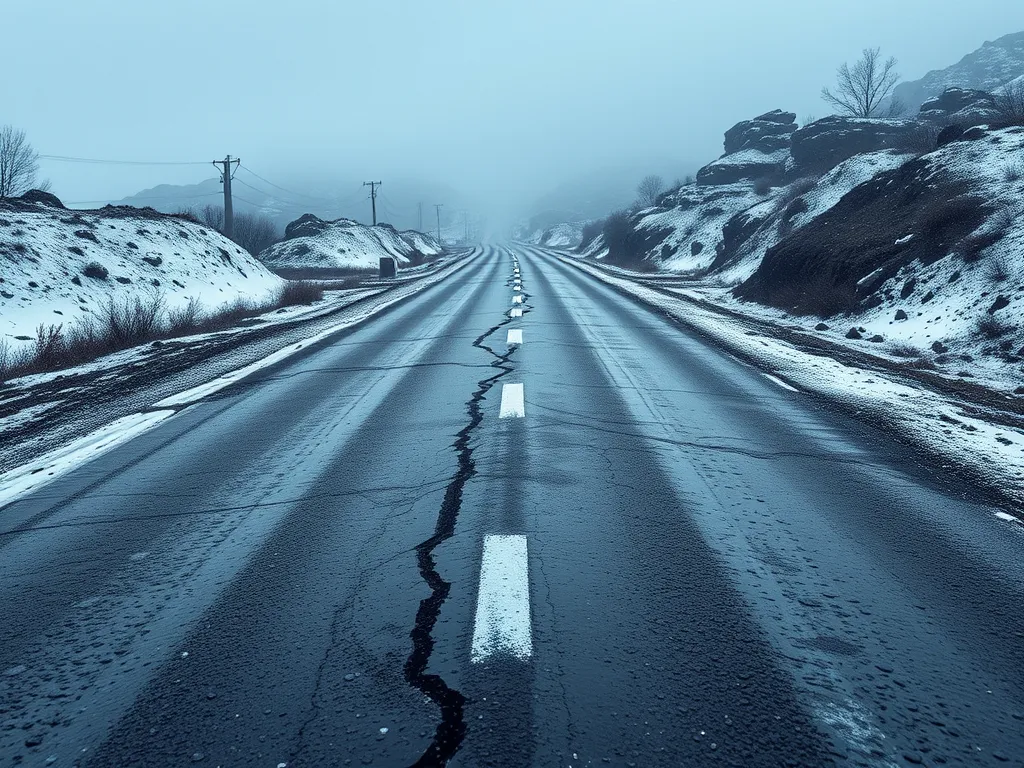
Implementing Advanced Testing Techniques
Translating theory into practice requires meticulous execution. Advanced asphalt pavement testing relies on precise workflows to ensure material performance aligns with design specifications.
Laboratory Procedures
Asphalt lab testing methods demand strict adherence to standardized protocols. Even minor deviations in temperature, timing, or equipment calibration can skew results by 10-15%, compromising project outcomes.
Sample Preparation and Conditioning
Proper sample prep forms the backbone of reliable data. Cores are cut to 150 mm diameters, compacted at 135°C±5°C, and cured for 4 hours per AASHTO T 168. Conditioning replicates real-world stressors like UV exposure (ASTM D4798) or moisture saturation (AASHTO T 283). Labs use gyratory compactors and environmental chambers to simulate decades of wear within days.
Quality Control Processes
Consistency separates functional asphalt from premature failures. Technologists run parallel tests on every third batch, cross-verifying metrics like air voids (4-8% target) or binder viscosity (3,000-5,000 Pa·s). Real-time alerts flag outliers exceeding ASTM D3666 tolerances.
Automation in Data Collection
Modern asphalt testing equipment integrates IoT sensors and machine learning. Pneumatic load frames now auto-record stress-strain curves at 100 Hz, while spectral analyzers map binder oxidation levels in 90 seconds. Cloud-based platforms like PaveSpec aggregate results across labs, slashing report generation from hours to minutes.
These streamlined workflows set the stage for balancing precision with ecological responsibility. Up next: minimizing environmental footprints without sacrificing testing rigor.
Environmental Considerations in Asphalt Testing
Advanced asphalt testing techniques now prioritize sustainability alongside performance. Labs balance precision with eco-friendly practices to reduce environmental impact while meeting ASTM and AASHTO standards.
Reducing Waste in Laboratory Testing
Modern labs cut material waste by 30-40% using optimized sample sizes and digital modeling. X-ray fluorescence (XRF) analyzers non-destructively test binder composition, allowing reuse of 90% of asphalt samples. Cold-in-place recycling (CIR) testing protocols validate mixes with 50-100% reclaimed asphalt pavement (RAP), aligning with ASTM D7229 standards. Automated mix design software minimizes trial batches, reducing aggregate and bitumen waste by 25%.
Energy-efficient Equipment Practices
Next-gen asphalt testing equipment slashes energy use. Variable-speed hydraulic loading frames in ITSM tests consume 15-20% less power than fixed-speed models. Infrared spectrometers for PG binder analysis operate at 50W—half the energy of traditional lab ovens. Smart rheometers with sleep modes cut idle energy drain by 60%. Labs adopting ISO 50001 energy management systems report 12-18% annual reductions in testing-related carbon emissions.
These green testing strategies prove environmental responsibility and technical precision coexist. As the industry evolves, data-driven methods continue to redefine sustainable pavement engineering practices. Up next: common questions professionals ask about implementing these advanced techniques.
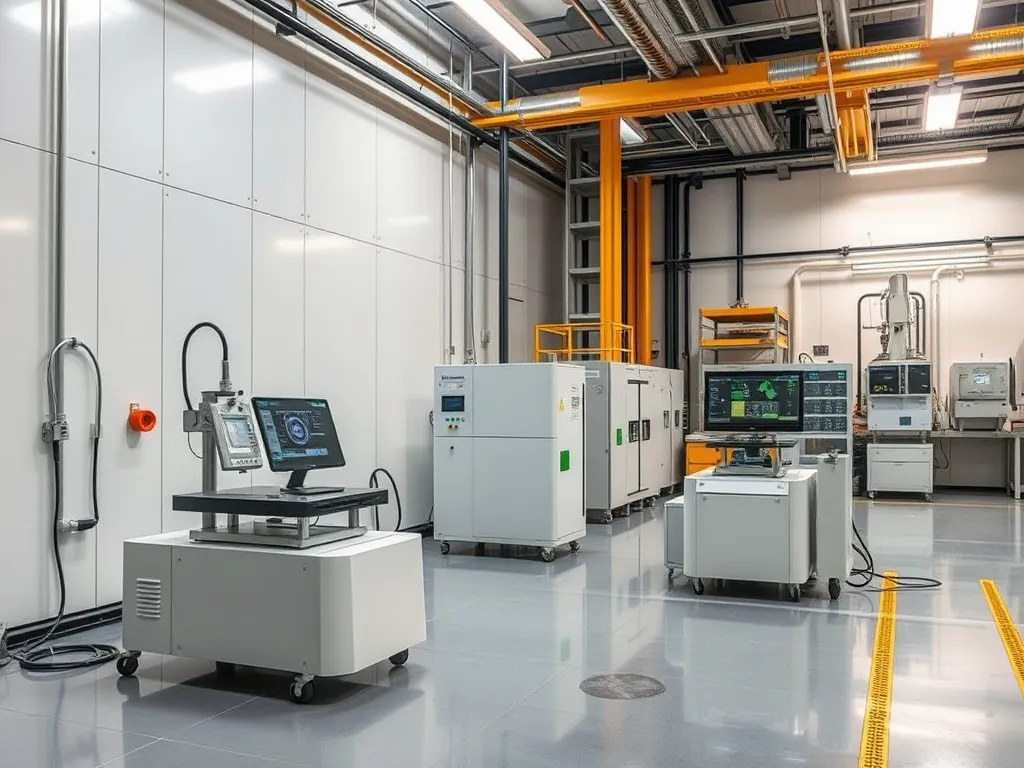
FAQ: Advanced Asphalt Testing Techniques
How Do You Test the Quality Of Asphalt?
Quality testing of asphalt typically involves a combination of laboratory and field tests. Common methods include dynamic shear rheometer (DSR) testing to assess binder properties, indirect tensile strength (ITS) measurements for mix performance, and field tests like the nuclear density gauge for compaction verification. These tests help ensure the asphalt meets specific performance criteria under various environmental and load conditions.
What is the TSR Test for Asphalt?
The TSR test, or Tensile Strength Ratio test, measures the moisture susceptibility of asphalt mixtures. It compares the tensile strength of soaked samples to unsoaked samples—calculating a ratio that determines the mixture’s ability to withstand moisture-induced damage. A TSR value of 80% or higher is generally considered acceptable, indicating good resistance to moisture-related issues.
What is the Marshall Test for Asphalt?
The Marshall Test is a method used to determine the optimal asphalt content in a concrete mix. It involves creating cylindrical samples that are compacted and then tested for stability and flow under specified loading conditions. This test helps assess the mixture’s workability, durability, and resistance to deformation, helping to ensure that the asphalt is suitable for its intended application.
What Are Some Environmental Considerations in Asphalt Testing?
Environmental considerations in asphalt testing include minimizing waste and energy consumption. Techniques like optimizing sample sizes, using non-destructive testing methods (such as X-ray fluorescence), and adopting energy-efficient equipment practices can significantly reduce the environmental footprint. Advanced labs also implement recycling protocols to reuse materials and ensure that tests meet both performance and sustainability standards.
Closing Thoughts
Advanced asphalt testing techniques play a pivotal role in ensuring the longevity, safety, and overall performance of pavement systems. By employing methods such as Dynamic Shear Rheometer testing and Multiple Stress Creep Recovery assessments, engineers can accurately evaluate the properties of asphalt binders. Tools like pneumatic loading frames and intelligent compaction analyzers provide essential data, helping to meet rigorous standards set by AASHTO and ASTM.
Moreover, incorporating environmentally friendly practices not only enhances the sustainability of asphalt testing but also contributes to a greener future in construction. By automating data collection, the industry benefits from improved quality control and efficiency.
For those interested in exploring more about asphalt testing or calculation tools, visit Asphalt Calculator USA for comprehensive information and resources.
Useful References for You:
- Lavin, P. (2003). Asphalt Pavements: A Practical Guide to Design, Production, and Maintenance for Engineers and Architects. London: Taylor & Francis.
- Asphalt Test for the Road Surface
- Asphalt Tests – Pavement Interactive
- Test Methods | Asphalt Testing Solutions & Engineering
- What is Asphalt Testing and Why Is It Necessary? – Aimil Corporate Blog